The Basic Principles Of Alcast Company
The Basic Principles Of Alcast Company
Blog Article
The smart Trick of Alcast Company That Nobody is Discussing
Table of ContentsFacts About Alcast Company UncoveredRumored Buzz on Alcast CompanyOur Alcast Company IdeasMore About Alcast CompanyThe 8-Minute Rule for Alcast CompanyThe Best Guide To Alcast Company
Chemical Comparison of Cast Light weight aluminum Alloys Silicon promotes castability by decreasing the alloy's melting temperature and improving fluidity during casting. Additionally, silicon adds to the alloy's strength and use resistance, making it important in applications where longevity is important, such as auto components and engine elements.It likewise improves the machinability of the alloy, making it easier to refine into completed items. In this means, iron adds to the general workability of aluminum alloys. Copper raises electric conductivity, making it beneficial in electric applications. It also boosts rust resistance and includes in the alloy's total strength.
Manganese adds to the strength of aluminum alloys and enhances workability. Magnesium is a light-weight aspect that provides strength and impact resistance to aluminum alloys.
The Best Guide To Alcast Company
It enables the production of lightweight parts with excellent mechanical buildings. Zinc enhances the castability of light weight aluminum alloys and aids regulate the solidification procedure during casting. It boosts the alloy's strength and firmness. It is often located in applications where complex forms and fine information are necessary, such as decorative spreadings and certain auto components.

The primary thermal conductivity, tensile toughness, return toughness, and elongation differ. Select ideal resources according to the efficiency of the target item generated. Among the above alloys, A356 has the greatest thermal conductivity, and A380 and ADC12 have the most affordable. The tensile limitation is the contrary. A360 has the finest yield stamina and the highest possible prolongation price.
More About Alcast Company
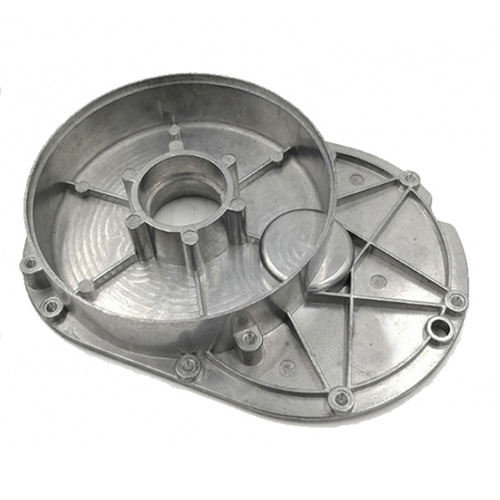
In precision spreading, 6063 is appropriate for applications where detailed geometries and top quality surface area coatings are critical. Examples include telecommunication enclosures, where the alloy's exceptional formability enables smooth and visually pleasing designs while keeping architectural integrity. In a similar way, in the Lighting Solutions sector, precision-cast 6063 parts develop classy and effective illumination components that require detailed shapes and good thermal performance.
It leads to a finer surface area coating and better corrosion resistance in A360. The A360 shows exceptional prolongation, making it excellent for complicated and thin-walled elements. In accuracy spreading applications, A360 is appropriate for markets such as Customer Electronics, Telecommunication, and Power Tools. Its improved fluidness enables for elaborate, high-precision parts like mobile phone cases and interaction tool housings.
Some Known Factual Statements About Alcast Company
Its one-of-a-kind properties make A360 a valuable choice for precision casting in these industries, boosting product longevity and top quality. Aluminum Casting. Light weight aluminum alloy 380, or A380, is an extensively made use of casting alloy with numerous distinctive qualities.
In accuracy casting, aluminum 413 radiates in the Customer Electronics and Power Tools industries. It's typically used to craft elaborate elements like mobile phone housings, camera bodies, and power tool housings. Its precision is remarkable, with limited tolerances approximately 0.01 mm, making certain remarkable item setting up. This alloy's premium corrosion resistance makes it an outstanding choice for exterior applications, guaranteeing durable, durable products in the discussed markets.
Things about Alcast Company
The light weight aluminum alloy you pick will substantially impact both the spreading process and the homes of the final product. Since of this, you need to make your decision carefully and take an educated method.
Establishing one of the most appropriate aluminum alloy for your application will certainly mean considering a broad range of features. These relative alloy qualities adhere to the North American Die Casting Organization's guidelines, and we've separated them into two classifications. The initial group addresses alloy attributes that impact the manufacturing process. The second covers characteristics impacting the buildings of the end product.
Alcast Company for Beginners
The alloy you pick for die spreading straight affects several facets of the spreading process, like just how very easy the alloy is to function with and if it is vulnerable to casting defects. Hot cracking, likewise called solidification splitting, is a normal die casting issue for light weight aluminum alloys that can cause interior or surface-level rips or splits.
Certain light weight aluminum alloys are extra vulnerable to hot breaking than others, and your selection should consider this. Another typical issue found in the die spreading of light weight aluminum is pass away soldering, which is when the cast adheres to the die walls and makes ejection difficult. It can damage both the actors and the die, so you should look for alloys with high anti-soldering buildings.
Deterioration resistance, which is already a remarkable attribute of aluminum, can vary substantially from alloy to alloy and is an important particular to think about relying on the ecological problems your product will be subjected to (Aluminum Castings). Wear resistance is one more property typically sought in light weight aluminum items and can distinguish some alloys
Report this page